Importance Of 5S In Six Sigma
I believe you all remember the article on 8 Fatal Lean Wastes. We spoke about eliminating wastes in order to add value to the customer. It is essential that this value chain is sustained over a period of time. It is also essential that employees continue to sort and organize their work and required resources in an effective manner on a daily basis. This is where 5S helps as a simple step-by-step methodology to ensure workspaces and resources are arranged and maintained in an orderly manner. Thereby enhancing productivity and reducing waste.
Let me pick an example closer home!
One day my 10-year old son was frantically searching for something in his study rack. He seemed to be getting at his wit’s end as he was unable to find it. I offered him help and we eventually found his geometry kit from within the rubble in his study rack. Although by the time he got the kit, he had lost interest in the geometry assignment which he was planning to start.
It is so exhausting and frustrating when we do not find what we need at the time we need. He looked at me with a resigned look. I suggested we could set it in order and fix it, if he can work with me. Having worked for an hour or so, we fixed the place and everything was set in order. As I was assigning spaces for books, stationery, craft items and others, he inquired out of curiosity. I told him, “Follow PEEP –Place for Everything, Everything in its Place!”.
Being a child and with his various commitments, he is tried to follow this as a maxim, till his age got the better of him!
However, in a work environment, you would realise that we cannot operate in a haphazard manner. It increases waste, reduces productivity, impacts delivery and above all, results in customer dis-satisfaction!
What is 5S?
Borrowed from Japanese and popularised by Taichi Ohno (designer of Toyota Production System) and Shigeo Shingo (associated with the concept of Poka-yoke).
5S is a set of 5 Japanese words starting with S. Translated into English, all the words start with S as well.
Let’s look at the 5S’s sequenced as a series of 5 steps* as follows -
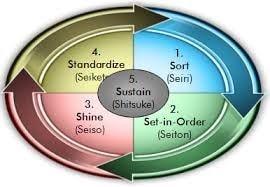
Step 1: Sort [Seiri]
In this step, the 5s concept practitioner has the responsibility to go through all the equipments, tools and resources they have and determine which equipment or resources have to be retained on the work floor and which resources have to be eliminated. When they find tools that are not relevant to their work they can simply place back that equipment to the storeroom or return them back to the concerned departments. If they feel that some resources need to be completely eliminated from the workspace, then they have to put a red tag on that particular item and get authorization or permission from their senior officials before they dispose it or recycle the item. In simple words, the practitioner has to segregate the important or useful things from the unnecessary thing and discard the unnecessary.
Step 2: Straighten or Set in Order [Seiton]
In this step, the 5S practitioner has to re-organize their workplace after eliminating unnecessary tools and equipment. Here the practitioner follows the simple philosophy of “a place for everything, and everything in its place”. This will help the other staff members locate the required resources easily and swiftly. This concept can be applied to any sector. In other words, the practitioner of 5S concepts arranges all the resources and tools in a systematic manner.
Step 3: Shine [Seiso]
In this step, the practitioner ensures that the equipment and tools are tidy and they can be readily used by other staff members. If this concept is applied in the information technology sector, then the practitioner has the responsibility to delete all the irrelevant files and folders and clean the file system. In simple words, this concept focuses on tidiness and cleanliness at the workplace.
Step 4: Standardize [Seiketsu]
The practitioner can combine similar work activities in their facility and allot a workspace for that particular process in the work facility. For instance, if there are five lathe machines scattered across different locations doing the same work, then the practitioner can place all these units at one place so that better results can be achieved through constant monitoring of work processes. This concept can be applied in any sector to reduce the redundancy.
Step 5: Sustain [Shitsuke]
This is the final step or stage in 5S concept implementation. In this stage, the practitioner has to ensure that tools, equipments and resources are in neat and tidy condition and they are placed where they are meant to be.
Where can I use 5s
5s can be applied in any industry – manufacturing, service, healthcare, public or private sector. As mentioned in my earlier example, it has got applications to a variable degree within our homes as well.
The following post-5S implementation pictures demonstrate the applicability of 5S in various environments.
Figure 1-Storage unit in an Office
Figure 2 - Laboratory in a hospital
Figure 3 - Tool box area in a factory
How can I apply 5S?
5S in various instances becomes the stepping stone for organizations looking to implement Lean within.
Let’s review the application of 5S in such organizations, as detailed in the pointers below.
1. Get all your employees to join the party!
Being a Leader and Lean Advocate, you understand very well that if people accept and own the same, application becomes smoother.
Choose a department or unit where you would like to do a complete 5S implementation. Workplace organization is the easiest and most obvious way to demonstrate 5S improvements visually, start with this. If yours is a data heavy unit, implement 5S for data storage and management.
Conduct 5S introductory or training sessions for your colleagues. Give them a post-training action to apply two of the tools at their workplace and report back as a team.
2. Seiri - Sort the workplace or storage space!
This should be treated as a waste reduction activity – eliminate unwanted things. Keep tools and resources that are needed frequently within reach. Review consolidation of workspaces to improve productivity e.g. combining all the lathe machines in one area reduces supervision.
In case of large amounts of electronic files on drives, eliminate the ones that are no longer needed. Archive files or information that is accessed infrequently.
Divide work into crack teams and let people within your teams lead the 5S implementation. The more they do it themselves, better the chances of sustenance.
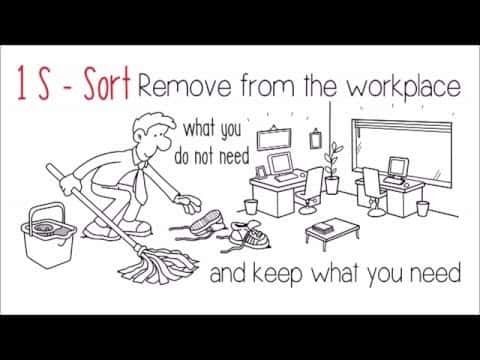
3. Seiton - Set the workplace or storage space in Order!
This step is about arranging everything in order. PEEP – Place for Everything and Everything in it’s Place.
Assign sections and spaces for different equipments, tools, and resources basis frequency of use. Ensure minimal maintenance and supervision. Blend mistake-proofing into the set-up.
In the picture above, note the sections created in line with the different tools. Any tool missing at the end of day or when required is a breach of process, which will be evident by observation. Thereby reducing waste and need for supervision and house-keeping.
Above picture demonstrates the scenario for a 5S compliant office desk.
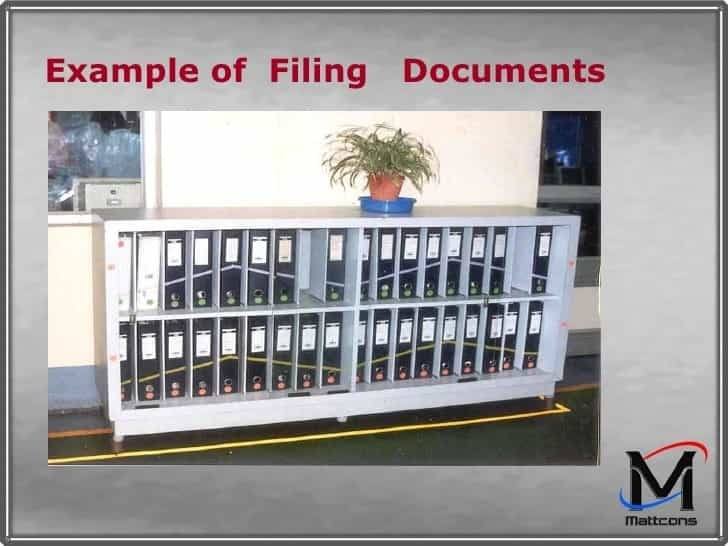
The filing cabinet above uses Poka-yoke or mistake proofing. On review, any file missing will break the tape-line sequence, thereby raising a red-flag.
For a virtual file system, define the directory structure. Define the types of files and data to be stored to the lowest sub-folder level. Ensure any file can be reached by the user with maximum number of mouse-clicks, say 3 clicks to save time on file access.
4. Seiso – Shine the workspace and storage system!
Tidy the workspace up and keep it clean. This is like going to a self-service restaurant. It is every individual’s responsibility to keep their workspaces clean and tidy.
No stray papers, no unwanted tools, files or equipment at the workspace. Review your workspace before signing off from your work day or shift. This is applicable from associates to managers at all levels.
In offices, ensure responsibility is assigned to people within your teams to check common equipment like printers. Ensure no unwanted papers are lying on any of the scanners or printers before end of work day/shift.
Get the teams to prepare a schedule of cleaning and upkeep activities through the year. Ensure one representative from each unit or team is responsible for adherence of the schedule.
5. Seiketsu – Standardize the workspace arrangement and storage protocols!
This is critical to the success of a 5S practice. Ensure all the processes related to Seiso are documented and understood by all.
The teams have defined responsibilities and timelines for the activities. As a leader and Lean Advocate, set expectations on when and how you would like to review the same.
Appreciate that this is new to the teams, so misses are bound to happen. Ongoing feedback and diligence will ensure it becomes a habit.
Use visual management and huddles as a means of instilling the culture further.
6. Shitsuke – Sustain the 5S practices!
You might have the best 5S initiative. Your teams might be enthused about all the action. But, there is always a risk of things fizzling out if let loose.
Ensure that leaders continue to speak to their teams on sustaining and maintaining the schedules and protocols documented and agreed.
Doing excellent work at Seiton and Seiso will be wasted if the agreed arrangements and protocols are not followed. Look at the picture below.
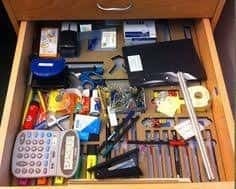
Conduct regular floor-walks; interact with teams to get a measure of how they feel about the new arrangements and protocols.
Get teams to do cross-audits and feed the same back to the respective teams. Be conscious about audits being improvement based and not gap-based. It is advisable to not widely publish audit results initially. Once majority of the teams have embedded the practices, doing so will be productive.
Most important, 5S and aligned practices have to be a part of the performance measures for every employee. Leadership has to constantly re-inforce and re-energize the practices to ensure sustainability over a period of time.
Let’s do it then!
Now that you understand how 5S can be implemented in your workplace, please get your teams warmed up to the same. Talk to them on the benefits of doing so.
The process is simple and has applicability across various spheres of business environments. Simple techniques like Sort and Shine can be applied within your workplace and homes as well.
Just to complete my 5S anecdote with my son – his drawer looks like needing some Sort and Shine again! I am not pushing him though! Please remember – it makes sense for people to join the party on their own rather than you forcing them to do so!
I hope you find this article helpful. Constructive feedback welcome!
Please use the discussion forum link below in case you have any points to add or questions to pose.
Learn more about Lean Methodologies directly from experts