5 Things you are likely to miss in the 5 Why Analysis
5 Why analysis also known as Why Why analysis is a powerful tool and extensively used for Root cause analysis across industries and geographies. 5 why analysis can be assembled effortlessly into any continuous improvement framework for effective problem-solving.
5 Why analysis aims at the permanent eradication of “highest level cause” of the problem that can cause nonconformance with the product or the service. The idea embedded in this tool is just simply asking the question “Why” until you reach to the highest level cause. Using 5 Why analysis is also important as it prevents teams from implementing short term solutions in the process.
I remember working with an engineer in one of my previous organization (Factory manufacturing food products), who use to solve all the breakdowns swiftly. Seeking the opportunity to learn from him, I started following him every time he went out to tackle the breakdown. After a few visits, I realized he has only one solution to each problem. He used to make a small block of sheet metal and weld it in the machine, whether it’s a leakage, vibration, breakage or anything else. Those were short term solutions and worked effectively till it deteriorated the machines to the extent where it became impossible to bring them back to their basic condition.
In such cases 5 Why analysis should be used to reach to the true root cause of the problem and to abolish it forever.
As stated earlier, since this is an extensively used tool, as per my experience with different clients and colleagues, I have realized that most of the time we miss 5 things while doing 5 Why analysis.
- A good start to 5 Why analysis means – “A precise problem statement”. As Charles F. Kettering says “A problem well stated is a problem half solved”. When we are able to define the problem correctly we are able to increase the depth up to which we can go to solve the issue. A bad problem statement creates confusion among the team and may lead toward the causes, which are irrelevant. We can use the tools like 6W2H to define the problem clearly before doing a 5 why analysis to get a good start. A typical 6W2H addresses below questions, which help in better problem definition:
-
WHAT – Description of the phenomenon, what do you see during the problem
-
WHERE – Transformation or the work point where the problem is taking place
-
WHICH – Is the problem specific to any particular product or service type.
-
WHEN – Is the problem specific to some time, weather, season, etc.
-
WHO – Is there any kind of variation among the teams or people
-
TO WHOM – What is affected due to the problem
-
HOW – What are the circumstances of loss/What is the failure mode
-
HOW MUCH – What is the magnitude of the problem (Number, frequency amount, etc.)
It is important to ask these questions and get the answers to define the problem. Sometimes the questions cannot be answered directly and it is important to collect the data or the information to get the right answers before. A problem statement prepared with these questions answered, will result in a good problem statement and eventually a good root cause analysis.
- A good team is vital to a good 5 Why analysis as the Root cause analysis is done on the problems where the solutions are not visible and there is a need of expertise to understand all the factors pertaining to the problem and then identify the highest level cause to eradicate it. A WOW team is the one which has “ETCH”.
-
Energy – Team consists of people who are passionate and constantly laugh or smile
-
Trust – Team consists of people who trust each other, are not afraid of asking questions or help
-
Clarity – Team consist of people who are eager to make things simple and easy to learn
-
Hearts – Team consists of people who vividly describes problems, pain or pleasures
-
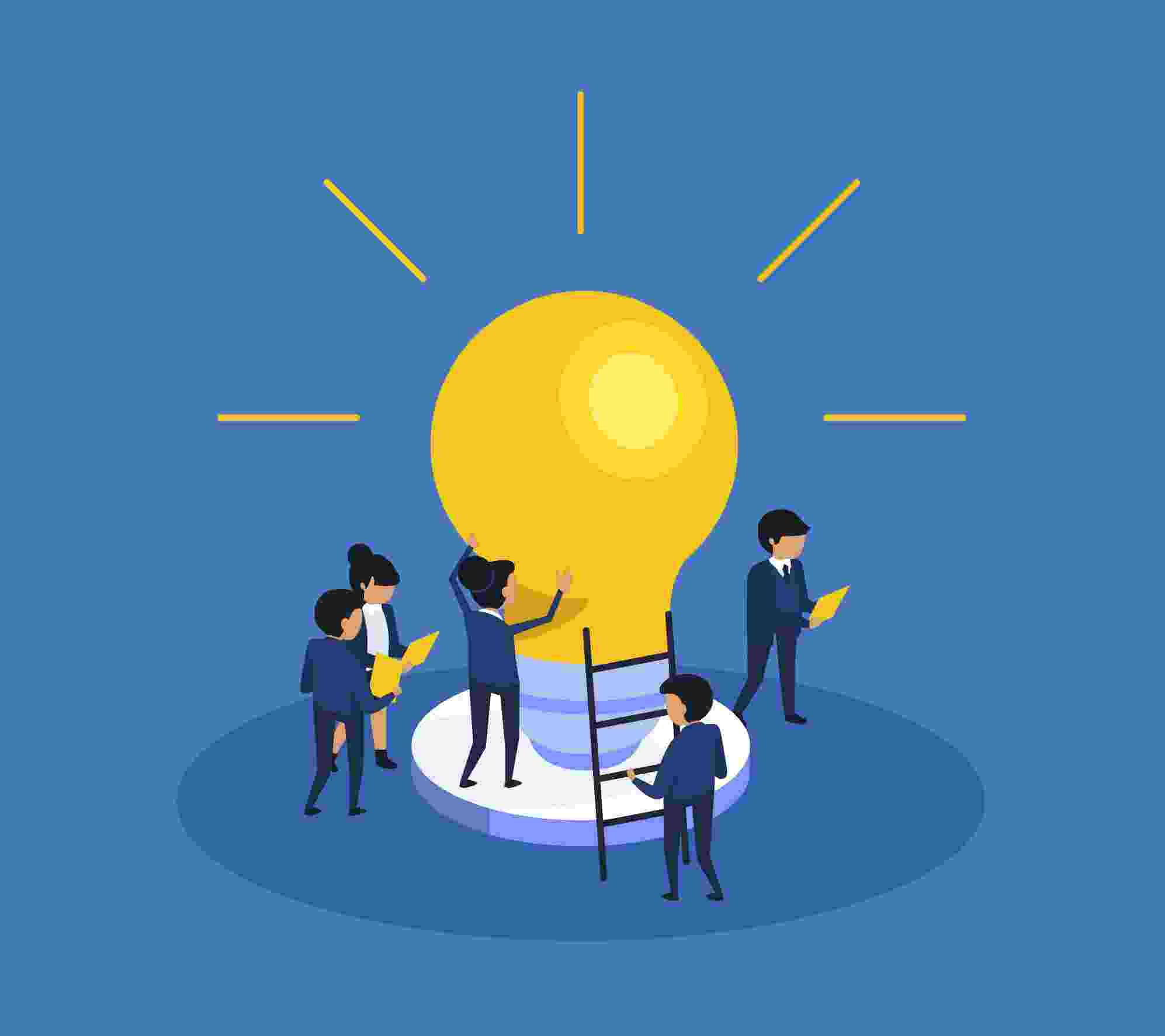
It is very important before doing a 5 Why analysis to have amongst the team
-
Clear goal (Subject matter experts, cross-functional teams)
-
Roles
-
Overview of the problem
-
Understanding of the procedures
-
Expectations within the team
A team identified with above-mentioned qualities will result in a robust 5 why analysis. When selecting the team, people should be from cross-functional teams, so that a complete perspective of the problem and the solution can be analyzed.
- Importance of field check, working with different clients and teams what I realized that this point is not taken care of most of the times. As 5 Why analysis is done with the team in the meeting rooms or discussion area, over a piece of paper or white/blackboard, we are not in the actual place where the problem is occurring. When we answer each why it is answered based on some assumptions or the knowledge/experience of the members of the team. Now, this makes it critically important to check every answer of why at the field (the place where the problem is actually occurring) and validate it with the help of the data/information.
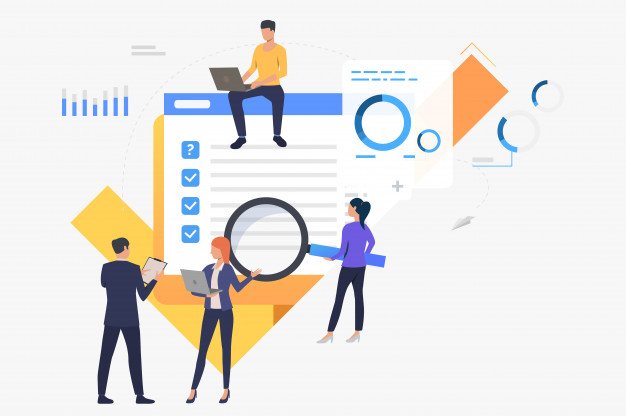
It is important to understand that the team who answer each why during a 5 Why analysis, they answer through their long term experience or knowledge from their academics. It has been seen and observed by many process owners that the actual process has a high probability of being different from what has been common knowledge and hence it is mandatory to check each answer of the why. Sometimes it is not possible to check the answer right away and need some time to gather data or information for that answer to be verified, in such cases we can apply a short term solution to prevent/decrease the damage till the answer to that why is validated.
For example, if an answer to a why is – “Because of the low temperature of the raw material this is happening”, it is recommended to collect the data of the temperature for that particular raw material with appropriate sample size and validate if the temperature is actually low or there is some other issue.
- Where to stop; It is a very important question and a lot of people that I have trained and worked with have asked me this question quite often – How many why’s we should ask, should we only ask 5 or can we stop at 3 or can it go up to 7. Now since there is no perfect answer to this question, I recommend one thumb rule to follow.
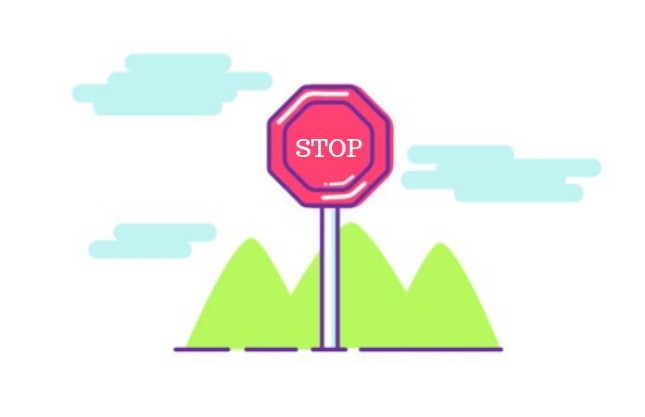
For every problem, always the reason behind is one of the below-listed issues
-
Poor Autonomous Maintenance (AM)
-
Poor Preventive Maintenance (PM)
-
Poor Design
-
Poor Standard Operating Procedure (SOP)
-
Poor Skill
So, when we are doing 5 Why analysis, we should look for one of these reasons to be the root cause, once we are able to reach here. It’s time to stop. Asking too many whys leads to the root cause that has nothing to do with the actual problem.
- Replication and Remedy; Replication is a very important part of the process in any 5 why analysis and most of the time it’s forgotten during the actual application of this Root cause analysis tool. Replication means reapplying the countermeasures obtained from a successful 5 why analysis in the processes, which may have a similar issue or possess the opportunity for the similar kind of defects to occur. This proactive approach saves time and helps the team to be prepared in case of such problem takes place again. Replication is also important as it sets the benchmark and help teams to avoid multiple efforts. This ability to replicate the solutions across all processes affects not only productivity but also the nature of the process itself. It makes the process
-
More reliable with lesser efforts
-
Enhance cross-functional knowledge of team members
-
Increase productivity among process and people
-
Below is an example of 5 Why analysis
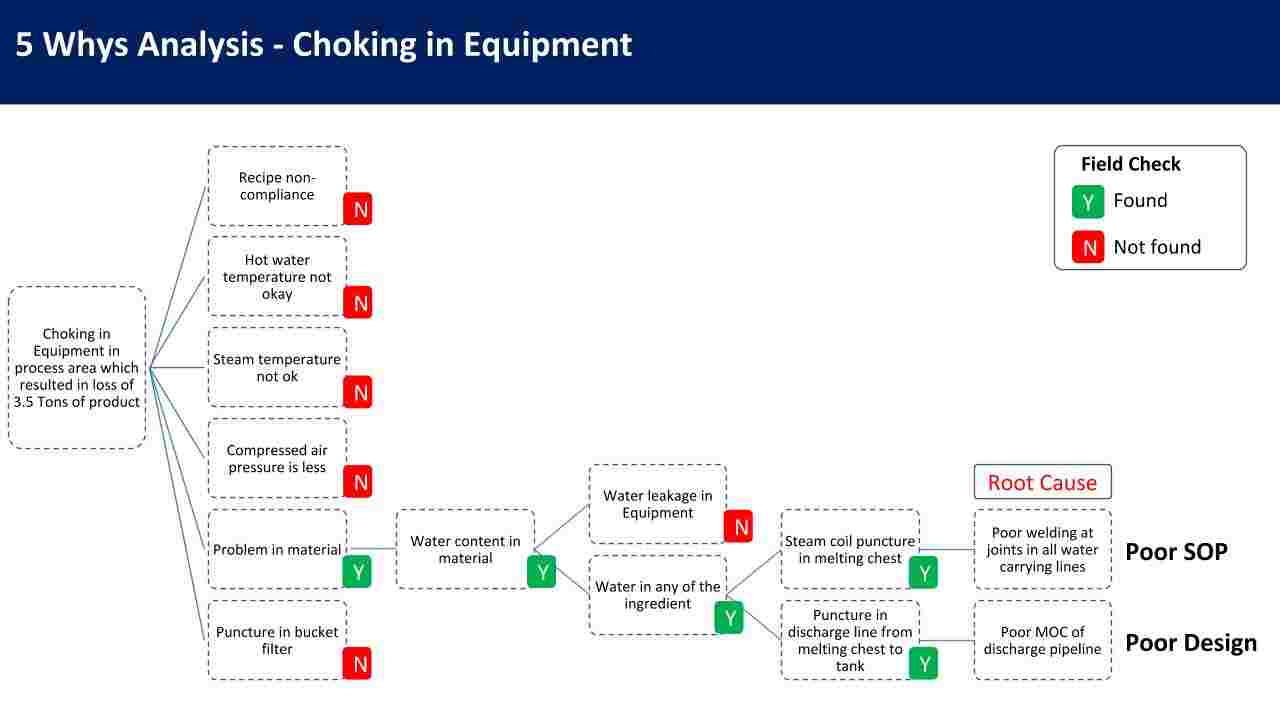
In the end, we can say that 5 why analysis is a robust tool and its effectiveness can be increased drastically if used wisely while taking into considerations above-mentioned factors. For the coaches, it is of prime importance that any 5 why analysis that is being mentored, is being done correctly and all aspects are well covered and taken care of.
Become a Quality expert. Get trained now!