How To Avoid Pitfalls In A Six Sigma Project And Deliver
Overview
Six Sigma is the methodology that improves the process by reducing variations in it. Businesses reap the benefits of Six Sigma in terms of money and customer satisfaction. Every businesses motive is to make a profit. Six Sigma has proved a successful methodology to improve the process.
Six Sigma improves the business process, and in turn, it makes the business to grow. By improving its process, a business can increase their profits exponentially. Six Sigma has many success stories to tell.
So, implementing a Six Sigma approach for the business process improvement is the latest craze in many industries to make a profit.
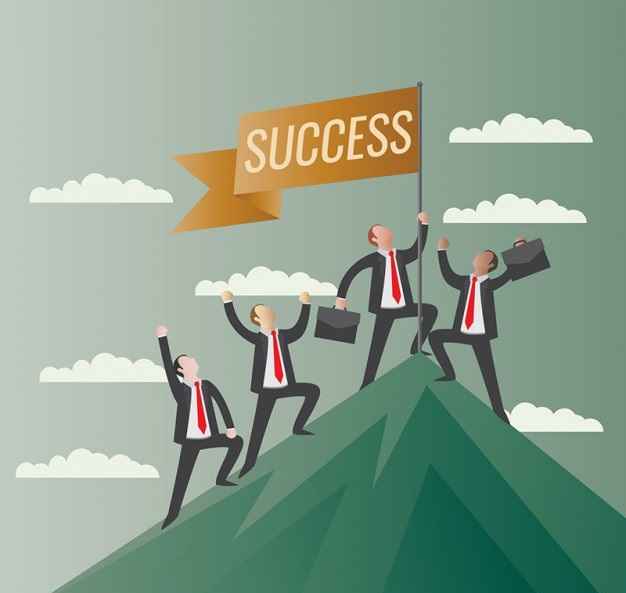
Six Sigma training has evolved as mature training programs with solid modules to improve the process. Businesses are following the streak to implement Six Sigma to improve the business. They are encouraging the employees to take Six Sigma training, and many companies provide the training in the house itself.
But they forgot to measure the fruitfulness of the training program. This makes the pitfalls in the Six Sigma projects. The six major pitfalls of the Six Sigma project are as follows and also the solution to avoid those pitfalls.
1. Expecting Quick Results
Six Sigma is rolled out in many organization in an unstructured manner. Six Sigma training is conducted as two or three-day classroom training program without any project related work. Given the craze of the program, the expectation of the training outcome is more.
The companies which give training to the employees expect them to produce Six Sigma projects as soon as they come out of the training classroom. They are required to make more returns within the month of the training, which is highly impossible. The company expects results without the proper launch of the Six Sigma program.
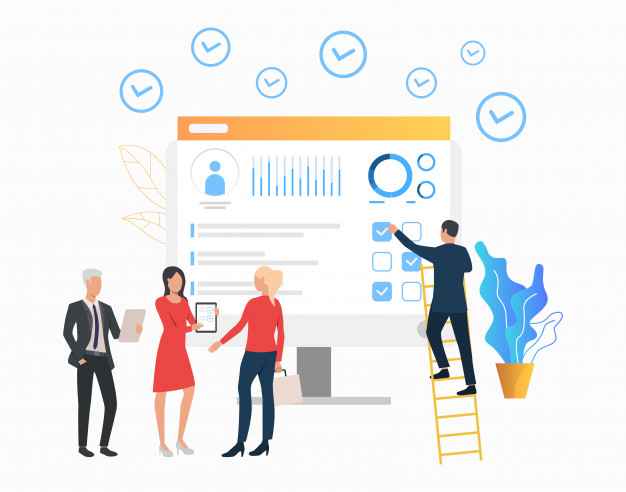
Solution:
Six Sigma implementation should be carried out in phases. Initially, the Six Sigma program can be launched as the small project with the help of Six Sigma consultant where the small projects are done by employees. Then, the employees are participated in small projects and provide a small saving for the company.
After a year, then each employee is required to do improvement projects in the company, thereby increasing the savings. Then after a year, formal Six Sigma team is formed inclusive of champion and black belts, and they monitor the performance of Six Sigma implementation and its results.
2. Business Goal Disconnection
Businesses’ path is decided by the business goals. Business with the best goals thrives as the best business. Business goal sets the pathway to the business improvement motives. If the organization goals are not set to clear by the organization, then the Six Sigma team end up in doing the project which is not aligned to the business objective. Six Sigma team may also take up a project which is not aligned with a business goal and end up doing the project, not improving the business process. This wastes time and resources of the organization.
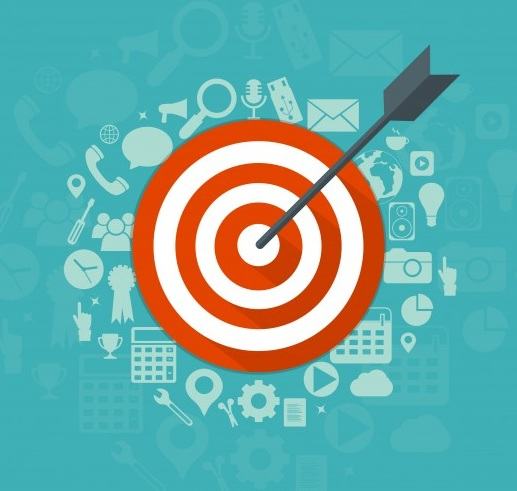
Solution:
The business goal is the key to business. Setting the business goal is the important task of the business to sustain in the market. Before launching the program, the organization must have a clear objective of the business. A company should make awareness about the objective of business to its employees. Then, the Six Sigma teams should have a black belt to lead the project and to align it to the objective of the business.
3. Failure of Measurement System
Six Sigma is a data-driven system. Data is the key to the Six Sigma system. To collect correct data, measurement of the data is important. So, measurement forms the foundation of the Six Sigma system. Having a valid measurement system makes the success of the Six Sigma project.
But very often, Six Sigma practitioners does not validate the measurement system. They are relying on the faulty measurement system. This happens due to the lazy nature of the practitioners to validate the system. They usually trust the appraiser for the face value. But as the Six Sigma practitioners, they must validate the measurement system to get more benefits from it.
Solution:
Six Sigma practitioners should always take time at the beginning of the project to check the measurement system. Validation of the measurement makes the data trustworthy. It asses the variation in the measurement process. Good measurement system forms the pillar to the project. This eliminates the problems due to the measurements and the measuring systems.
4. Selecting the wrong projects
Six Sigma is a proven methodology to make improvement in a defined way. To reap the benefits of the Six Sigma very quickly, the companies urge the Six Sigma team to take up the projects that are out of their expertise. This will make the project go out of control. This incorrect selection of the project may end up the resource to utilize their skill on an unwanted project.
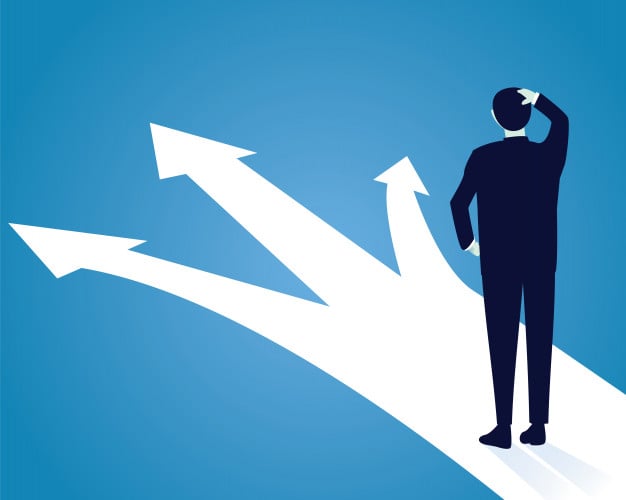
Solution:
Making a high standard on selecting a Six Sigma project before starting the implementation. This helps the business to prevent resource wastes on the process improvement project that are likely to fail. Six Sigma project selection should be data-based and prioritized focusing on goals. To select the Six Sigma projects, use Standards such as the impact on business goals, measurable business benefit, clear process improvement, and high customer satisfaction.
5. Lack of Management support
Full support of the management for a Six Sigma project is very important. The Six Sigma project success is based on the support of management and leadership to the project. Lack of management support will turn improvement process meaningless.
Lack of leadership to the Six Sigma project will make the project go in vain before even it starts. This discards all works of the resources. Without proper leadership support, the team will not know the path of the project.
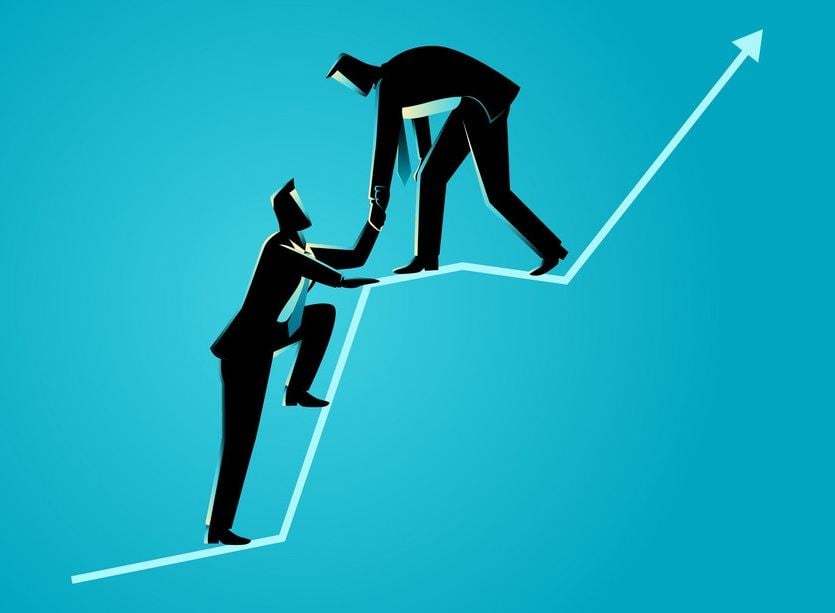
Solution:
Management should make a commitment to the Six Sigma improvement project. Management should appoint an experienced project champion and Black belt to lead the Six Sigma implementation and to manage the Six Sigma project progress.
6. Avoiding Stakeholder involvement
The Stakeholder or the process owner who works in the process in day to day work. Often, Six Sigma green belts avoid the help of process owners in the project. They will not get suggestion or inputs from them for the project progress. But the process owners are the bank of practical knowledge. They help the project in identifying problems and providing a solution to it. Six Sigma team get experience in the process with the help of process owners. Without practical expertise, teams can only give a theoretical solution to the problems.
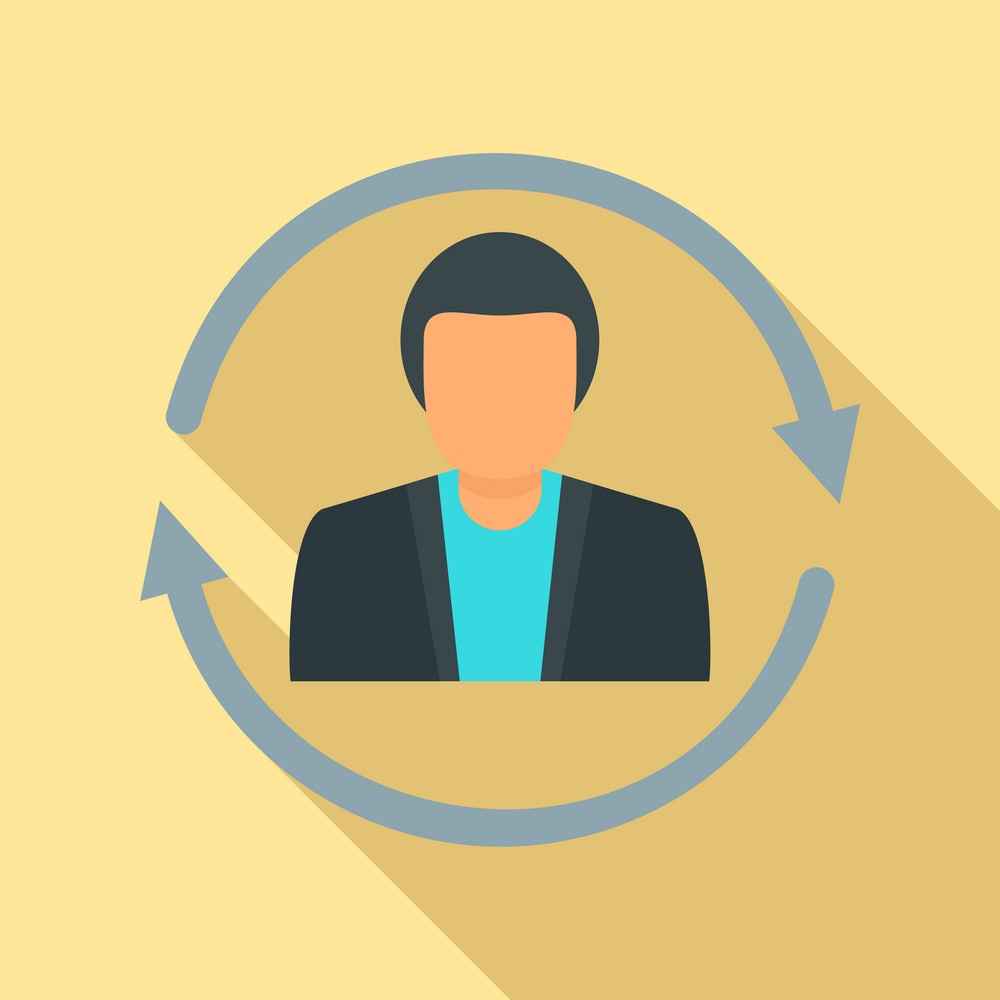
Solution:
Six Sigma practitioners will understand the process better when they include the process owner in the project. One should take a Gemba walk to understand the process. They will know better than the one who reads on paper. So, the Six Sigma practitioner must include the process owners in the project.
7. Overtraining
Not every officer of the peace corps needs to have SEAL training. Likewise, not everyone on the Six Sigma implementing company needs to learn every statistical tool of the Six Sigma.
The Six Sigma courses are boomed left and right. Six Sigma trainer and consultants are competing with each other to capture the market. But the very fewer people use the Six Sigma tools regularly in life.
Expecting to use every tool in the Six Sigma project you learned is foolishness. Learning more and more tools may end up in confusion. Study says that 80% of the people are engaged in trying to get benefits of less than 20%.
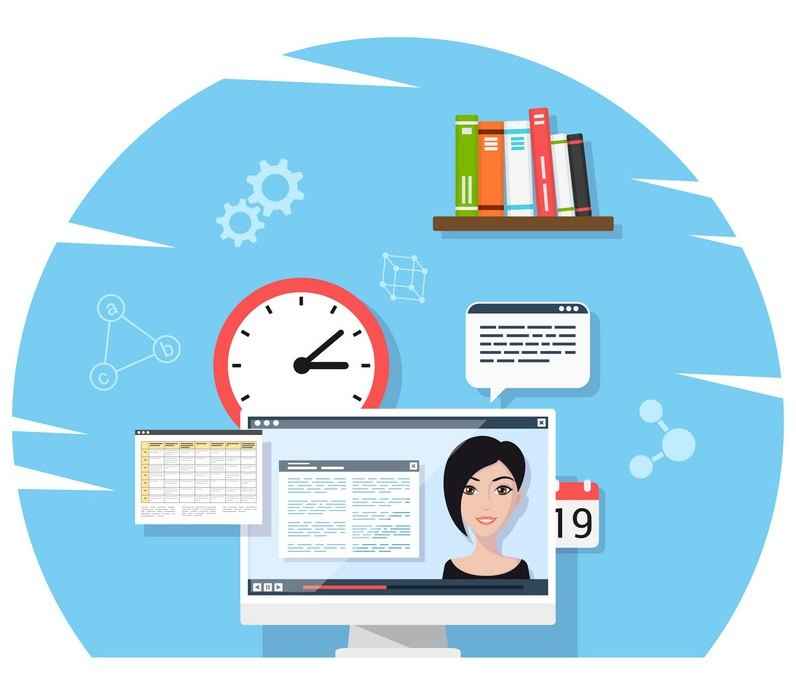
Solution:
Training more doesn’t mean doing more. Implementing what you learned in Six Sigma training class may help to get more benefits out of the class.
The disadvantage of Six Sigma
Like any other methodologies, Six Sigma also has its failures. It may also produce poor results. Six Sigma projects produce a poor result when the business strategy is against the Six Sigma progress. To overcome these pitfalls, select the relevant projects aligned to the business goals. Then validate the measurement system very stringently, since Six Sigma is data-driven it is based on data.
Management can overcome the pitfalls by having extensive leadership support and dynamic team with process owner. Management should expect the results of Six Sigma implementation only after the maturity of the Six Sigma system in the business.
Six Sigma inspects minute-by-minute company processes and produces big quantities of empirical information, resulting in time-consuming and complex procedures. Also, because at its root, it is a method of quality improvement, adopting its protocols often leads to a rise in overall costs.
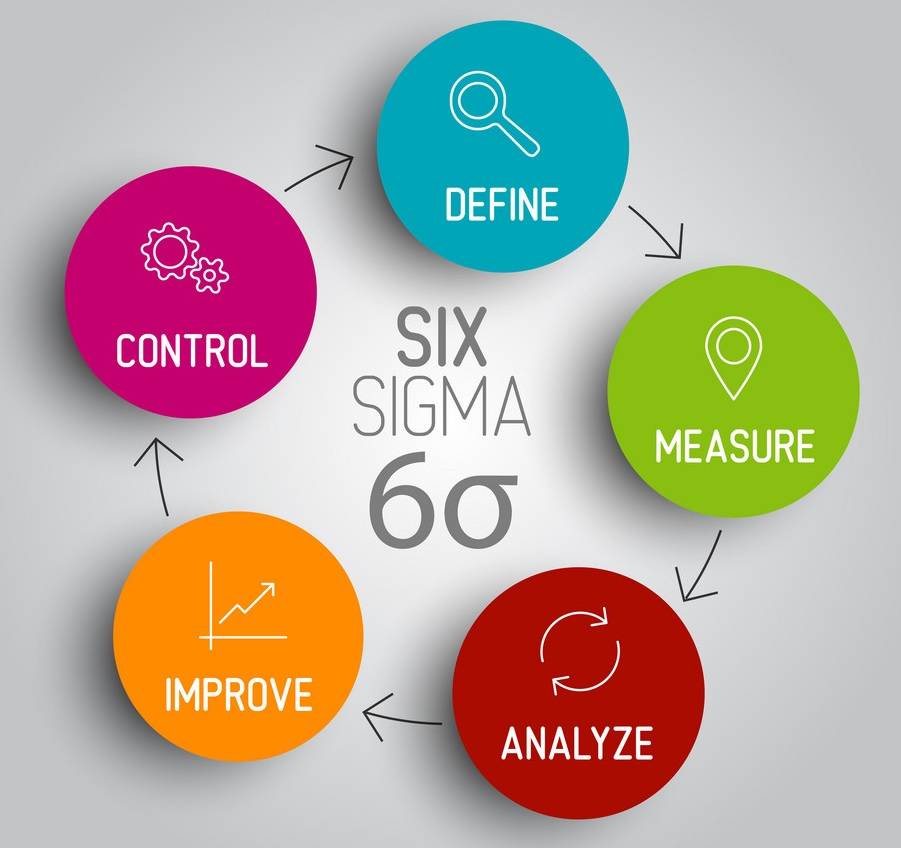
Sometimes problems arise when a company implements Six Sigma as the company focuses only on Six Sigma policies that have been endorsed and forgets its specific mission statement or policies. It may restrict fresh thoughts in favor of creativity and innovation for small companies that require some risk-taking to be implemented. Small companies have to find Six Sigma trainer and have the training without any formal certification, which is costly for small businesses. Adoption of Six Sigma is too high.
If the above-mentioned steps are put into practice, then you can avoid the pitfalls in a Six Sigma project. The focus must be on improving the process and delivering high-quality results. This is the ultimate goal for any project manager with a Six Sigma Black Belt certification.
Stabilize your process | Sign up for a Six Sigma course now!