PDCA Cycle and its Application in Healthcare Industry
Brief Introduction
PDCA is one of the most commonly used tools for organizing the operations of an organization. It has gained importance in many different fields of work. The healthcare industry has made this approach an integral part of its management system. A healthcare facility can truly benefit through the PDCA approach.
What is PDCA?
The PDCA (Plan-Do-Check-Act) was first presented by Walter Shewhart in 1929 and promoted by W. Edwards Deming in the 1950s as a flow graph for learning. Deming supported the use of PDCA as a persistent feedback loop to break down, measure, and recognize sources of variations from client requirements. This was to initiate corrective measures.
Origin in Scientific Methods
Plan
The planning stage includes evaluating a present procedure, or another procedure. Then it is about making sense of how it can be enhanced. In this stage it is essential to realize what sort of yields are necessary. Further plan is built up to settle the procedure. Usually it is simpler to design little changes during this period of the planning. With this, the goal can be effortlessly monitored. The outcome itself becomes more predictable this way.
Do
The do stage permits the plans from the past advancements to be brought into action. Little changes are usually tried. The information is gathered to take a deeper look at how powerful the changes may prove to be.
Check
In the check stage, the information and results accumulated from the do stage are assessed. This information is contrasted with the normal results to observe any significant differences. The testing procedure is likewise assessed to check if there were any progressions from the first test. This first test was made in the planning stage. The information is placed in a diagram, this makes it easy to observe any perceivable patterns in the PDCA cycle. This is if the PDCA is conducted repeatedly for certain number of times. This way, the changes that work well in comparison to the others can be observed. Also, the said changes can be further enhanced too.
Act
The check stage demonstrates that the plan stage, which was actualized in do stage is a change to the earlier standard (benchmark). At this point it turns into the new standard (pattern). It is at this time that the organization should go ahead with the new guidelines, which are to be acted upon. Sometimes, the check stage shows that the plan stage which was executed in do stage isn't a change. At that point the current standard (gauge) will persist. In either case, if the check stage demonstrated something other than what was expected, some more investigation is needed. Potential future PDCA cycles are recommended.
Learn more Lean Six Sigma methodologies: How do they improve Health Care industry?
Example of PDCA at the Healthcare Facility:
Plan
-
I want to test a procedure of collecting patient satisfaction survey.
-
The test must produce no less than 25 finished surveys for each week during the tenure.
Steps to be executed:
-
The surveys shall be displayed at the checkout desk.
-
The checkout personnel will urge the patient to take the survey. They will be requested to fill the survey at home and mail it back.
-
This will be attempted for a duration of 2 weeks.
Do
What did you see?
-
The checkout personnel effectively worked on the request of the survey into the checkout process.
-
We saw that the patient had different papers to handle at the time.
-
Per checkout personnel, only around 30% patients took the survey.
Check
What is learnt? Was the measurement objective met?
-
We just had 3 surveys returned towards the finish of the 2 week period, the process did not work as per expectations.
Act
What did you understand from this cycle?
-
A few patients did not want to be pestered at this point of the visit. They wanted to check out, not take a survey.
-
Once the patient leaves the building, he/she will probably not take the survey.
-
They have to be approached during another point in their visit to the hospital. This could be at a point where they are in the waiting area, and they have nothing much to do.
Explore Six Sigma Applications In Healthcare
Importance of PDCA in Quality Management of Healthcare
- Reduces Error
The healthcare industry is such that, the chances of error are huge; efficient planning reduces such chances of error. Adoption of this tool largely eliminates mishaps in the healthcare operations. It enhances the quality of delivery for the patients. It also brings ease to the management of operations in a hospital or a healthcare facility.
- Prevents Shocks and Surprises
The PDCA cycle in the healthcare industry prevents shocks and surprises in many ways. For example, the PDCA cycle can ensure that there is sufficient stock for a healthcare facility to run. During a surgery or operation, the PDCA cycle helps in its smooth accomplishment.
- Identifies Problems
The PDCA cycle successfully identifies the glitches that exist in the process. This happens in the plan stage of the PDCA cycle. When the PDCA cycle is run repeatedly, many such problems get eliminated from the process. This brings in efficiency and effectiveness.
- Modifies Existing Processes
The existing process is further modified with the help of PDCA cycles. This reduces the chances of technological and operational obsolescence. Modification and updating is of utmost importance in the healthcare industry. Medical equipment faces a lot of technological development as the years pass.
- Lean
The PDCA cycles contribute to inculcating lean in the process. It minimizes waste to a large extent, the problem of waste in the healthcare industry is certainly a nuisance. There are a large number of medicines which expire; and resources like water, cotton and needles need the right environment for their durability for medical purposes. The inculcation of lean through the PDCA cycle maintains such factors in healthcare.
- Continuous Testing
Continuous testing takes place through the PDCA cycles. This is done through the do stage. This testing brings out the adept practices that a healthcare management should follow.
- Ensures Cash Flows
The healthcare industry apart from its human aspect serves as a profit making venture. If the patients are looked at from the customer point of view, then the PDCA cycle ensures a good name in the industry. It brings in more footfall as the patient’s belief in the facility strengthens.
Comparison and connection of PDCA to other methodologies like DMAIC, Lean, and ISO 9001
The PDCA is a process focussed approach which brings in continuous planning, doing, checking and acting upon. This method is adept for short term observations. The PDCA technique might often be used for long term observations as well.
DMAIC is a six sigma approach, it stands for define, measure, analyse, improve and control. These five phases contribute to the overall quality enhancement of an institution. This methodology is adept for a manufacturing unit. The DMAIC methodology can be applied in a versatile manner, there is no hard and fast rule for its application. However, in the healthcare industry, the application of DMAIC methodology might need the project manager to have some idea about the fine aspects of the health industry.
The ISO 9001 can be defined as a benchmark for quality. Enhancing the quality and upgrading the patient’s safety through a defined quality management framework. It is the most ideal approach to give a patient focused care. ISO 9001 gives a model to the quality management framework, which stresses on the viability of clinical, business and support procedures to guarantee excellent care. The standard advances the appropriation of a procedural approach; this emphasizes the necessities, adds value, process execution and effectiveness. Also, continual change through target estimations brings in quality improvements.
Past variants of ISO 9001 were custom fitted to the assembling ventures. They were called for broad framework documentation. The present form is more non-exclusive and can be connected to associations of any size and industry. It is undeniably perceived as an appropriate standard for social insurance associations, which desire to convey great, quiet focused human services.
However, all of the above approaches have the same motto, that is to bring out the best in an operation.
Application in Healthcare
Example 1: The Clinic
In an eight state rural supplier of consultation providers, it takes nine days from a patient's first telephone call until the point when he is evaluated for treatment. An organization’s official notified that 71% of booked patients appear for their treatment. The official composes this as, "It takes nine days to get treatment and just 71% of patients appear." For the Plan, it is modified as, "In three months, it will take three days to get an evaluation and 90% of patients will appear". This was as per their needs to be surveyed, and also changing staff timetables to comply with their requirements. A particular staff individual is assigned to guarantee that; whatever number of spaces as could be expected under the circumstances are filled every day. During the procedure, issues with the telephone framework were found. These issues were tackled successfully.
In four months, the normal period of time between a telephone call and treatment was reduced to five days. The no-turn up rate also dropped, and there was a sudden reward- a record increase in the achievement rate was seen for the patients.
Related reading: Top Reasons For Using Six Sigma in Healthcare Industry
Why adopt PDCA?
-
PDCA brings in continuous change, it is implemented in a manner that the process is modified and made adept at cost reduction, profit maximization and increased patient satisfaction.
-
This continuous change prevents obsolescence. As the environment today is dynamic in every possible manner, there is a need for updating the techniques and processes as frequently as possible. The devices used in the medical industry are evolving by the day. Under such circumstances the obsolete devices should be disposed at the earliest. New peripherals and medical devices always bring more efficiency and patient satisfaction.
-
With the passage of time, it brings things in order. As time passes by, the PDCA is implemented at regular intervals. The results of each implemented PDCA cycle are recorded. On the basis of the differences in the recordings, things are brought into the adept order.
-
Many a times the management might believe in certain processes, the PDCA might challenge this belief. Organisations at times believe that their adopted process is nothing less than state-of-the-art. In reality, such process might be taking up their major resources and providing least output or yield.
-
The already established process has been improved further. As a process checks through the PDCA stages, one is able to successfully observe the small loopholes and benefits of the process. The study of these processes will bring out the best in an organization.
-
PDCA has time and again proved its efficiency in companies like Nestle, Lockheed Martin and Toyota. These companies have implemented it as part of their Kaizen. The world has stood witness to the growth and expansion of these companies. We can also see that these companies have effectively been able to produce quality products without variation.
Adaptability to Quality Control
The PDCA cycle is widely used in companies as a part of their Kaizen. This is because of the tool’s contribution towards improved quality standards. In the diagram below, we can see that how PDCA’s different stages have ISO’s quality management principles.
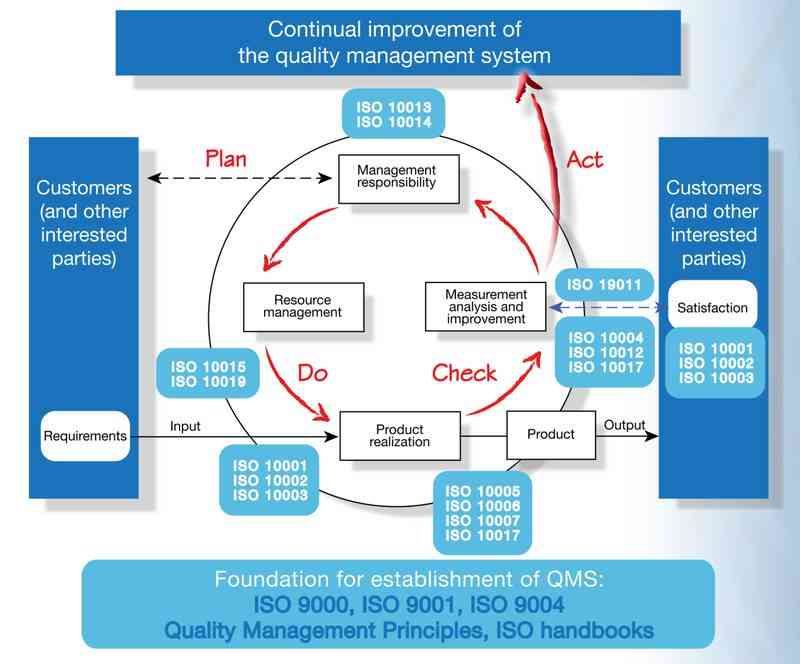
Image Source: https://creativesustainabilitymarketing.wordpress.com/2013/03/20/iso-standards-the-iso-9000-family/
Conclusion
Adoption of the PDCA cycle in the healthcare industry will have a plethora of benefits. It is a win-win situation, where the patients and the hospitals get the best possible results; procedures take a leaner shape. The efficiency of the management also increases as the processes become hassle free and smooth. The tool has had a significant presence in many industries, and can yield exceedingly good results in a healthcare facility.
Click here to accelerate your career in Quality Management
Other blogs from the author: Top Quality Management Tips to Enhance Your Business Performance